
Unscheduled repairs are always more expensive and typically result in downtime that negatively impact on your company’s ability to do business.
#Defect process drivers#
With the telematics information that is now commonly available from onboard systems, you can identify drivers with a tendency for unsafe behaviours, such as speeding, rapid acceleration or hard braking, and then create better drivers by acting on that information with coaching and training. Pinpointing problems and working to address them can improve your defect management process, but can also benefit your fleet’s safety performance. For example, if your fleet or a group of vehicles is experiencing a large number of specific component failures after a certain mileage interval, a maintenance or replacement campaign can offset future failures. Asking questions about high cost categories for vehicles, systems and components helps you identify areas that require attention. Working with the vast information inside defect management software is the first step towards avoiding defects. With these initiatives, you can greatly improve fleet efficiency and reduce unscheduled downtime. Breakdowns and the downtime to remedy these problems can lead to higher costs that can negatively impact on both employee and customer satisfaction.Įffectively managing your defect management process is about getting ahead of the issues by applying proven practices. Unscheduled repairs are one of the mostly costly fleet management issues. But if your defect management system isn’t covering the basics, your fleet can suffer.

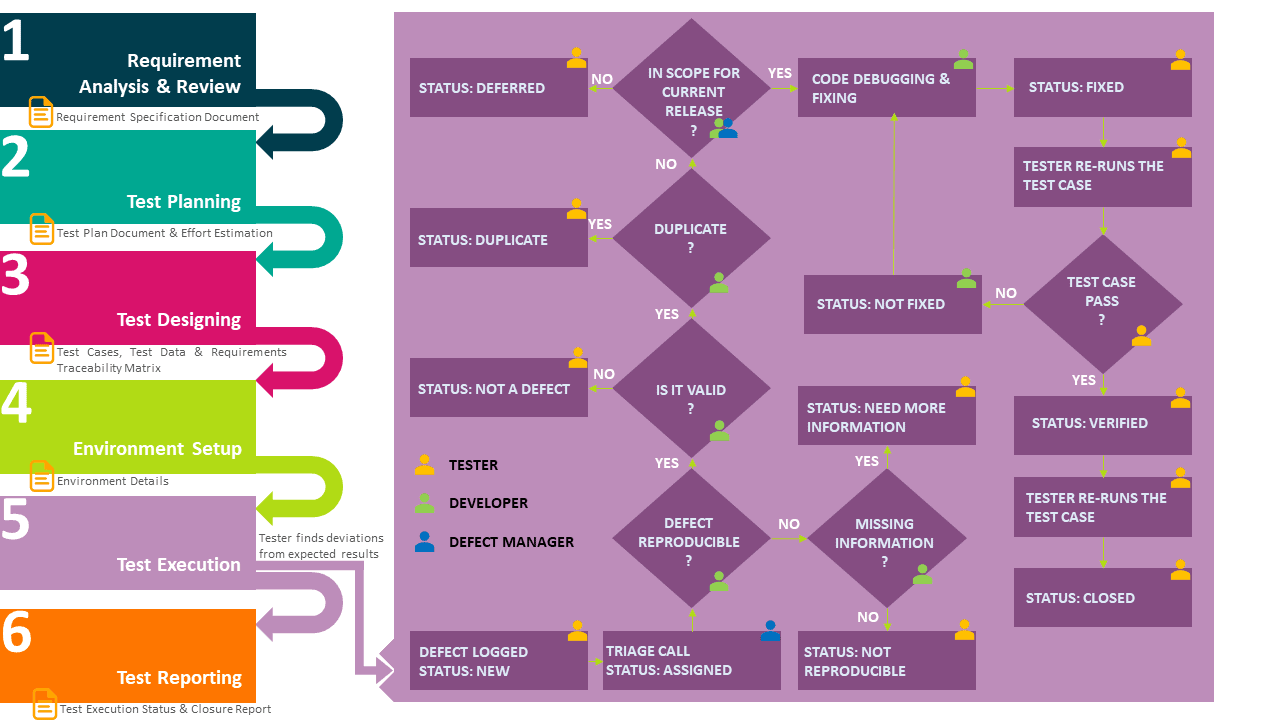
Managing defects can help ensure compliance as well as preventing unscheduled downtime. How up-to-date is your fleets’ defect management process?
